Tour the CAPS Facilities
FSU-CAPS brings unique capabilities to the research and development community, with a specially designed facility and a high-caliber research team recruited worldwide from academic institutions and industry organizations. Members of the Facilities Group support the Center’s research activities. Our team includes highly qualified engineers, designers and technicians with experience in the fields of electrical power engineering, mechanical engineering, cryogenics, process control, system engineering and data acquisition. They are responsible for carrying out the unique experiments undertaken by FSU-CAPS researchers as well those performed for our industry clients.
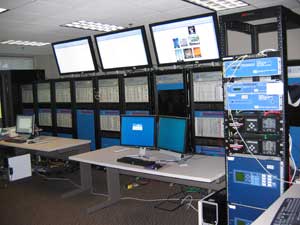
Digital Real Time Simulator (RTS)
Digital Real Time Simulators are special-purpose multi-processor computer systems designed for coupling power system simulations to the physical world. This real-time simulation coupling means that the simulated system advances synchronously with wall-clock time every time step. For power system simulation, time steps in the 10s of microseconds and lower are typical. In a low risk yet realistic environment, the RTS allows testing a critical electrical grid without actually turning off the lights around the nation or putting a ship in harm’s way.
5 MW Prototype Test Facility
CAPS offers a state-of –the-art test facility for evaluating prototype electric machines and devices. The facility couples real hardware with the largest Real Time Digital Simulator (RTDS) installation in any university and one of the largest capabilities for real-time power system simulation and modeling available anywhere in the world. This marriage of hardware and simulation provides a unique, Hardware-in-the-Loop (HIL) test capability unmatched by other research facilities.
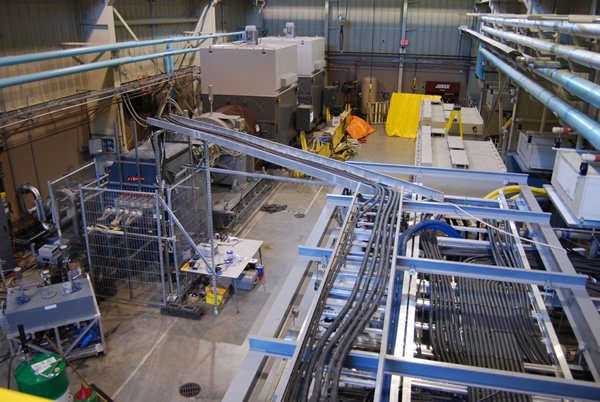
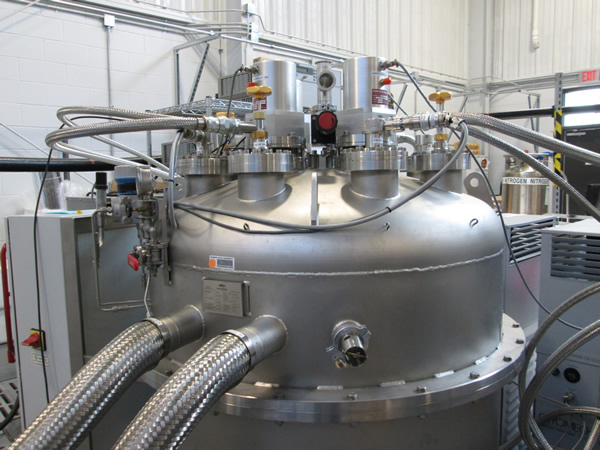
High Temperature Superconductivity and Dielectrics Laboratories
Electric power devices that use high temperature superconducting materials instead of copper offer significant improvements in the capacity, efficiency, and reliability of electrical systems. At CAPS, we are pursuing the powerful science and technology of superconductivity. We have established a suite of advanced experimental, modelling, and simulation tools to support the development of superconducting power devices. We have a high-voltage laboratory for developing dielectric systems suitable for cryogenic operating temperatures of superconducting power system components. We focus on the research, development, and design validation of prototype high temperature superconducting power system components for electric utility and transportation applications through collaboration with industry.
Power Electronics Laboratory
The Power Electronics Laboratory at FSU-CAPS is equipped with the state-of-the-art hardware for both low voltage and high voltage converter development. Lab equipment supports modeling, analysis, simulation, control design, and prototyping implementation. Recent success stories include medium voltage modular muti-level converter technology that is ready for a digital overhaul of electric distribution systems, supporting the integration of large amounts of distributed energy generation and storage solutions into power grids.
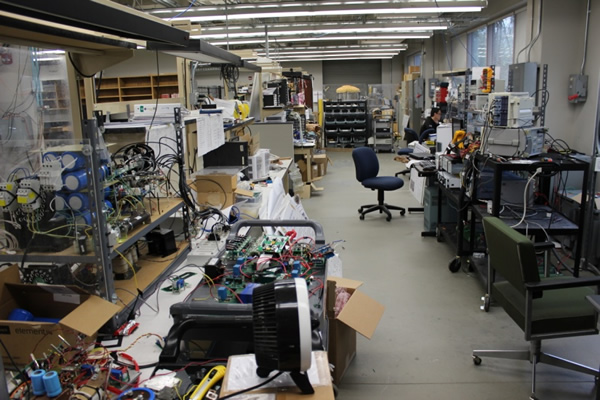
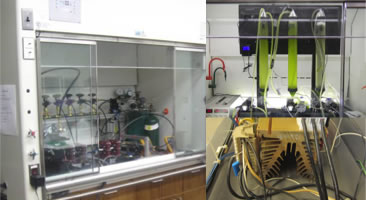
Thermal Systems Laboratory
This lab provides capabilities for thermal measurements (flow, temperature, pressure, humidity) for a diverse set of configurations relevant to the thermal evaluation of power systems. For flow measurements we have ultrasonic systems, Pitot, rotameters and paddle wheel sensors. For temperature, we have custom data acquisition systems for thermistors and thermocouples readings, infrared devices for non-contact measurements. Additionally the lab has capabilities for fuel cell testing, microalgae growth (including growth monitoring via spectrophotometer and optical microscope), and solar irradiation measures (direct and diffuse) for solar applications.
Cyber Physical Systems
The integrated real-time simulation capabilities at CAPS provide unique opportunities for research in the field cyber-physical systems (CPS). These capabilities are categorized into to two major subsystems. The first subsystem is a set of highly reconfigurable electric, thermal, and mechanical testbeds that seamlessly integrate with a set of general-purpose controller boards which can host software code to experiment with truly distributed (i.e. agent based) control approaches. Moreover, the lab is integrated with the RTS environment at CAPS such that it fully supports all types of HIL simulations.
The second subsystem consists of another cluster of controller boards which, by virtue of a high bandwidth data channels, allow those controllers to communicate local control signals to power electronic sources and loads simulated on the RTS. The high-level control communication between the controller boards can be either routed through a multi-function switch or through a real-time simulation environment. The latter allows simulating the behavior and characteristics of the communication between distributed control processes to study the effect of communication backbone changes on the power system simulation.
Together, these two subsystems provide a unique environment where researchers can experiment with systems composed partially in hardware and partially in simulation. It includes the higher-level processing/intelligence, communication interface and control layers necessary to study various distributed control algorithms applied to DC and AC microgrids. Distributed control nodes (DCN) are implemented for each of the sources, distribution, and loads to provide higher-level functionality/controllability and to facilitate node/load centric control strategies. This establishes a standard system platform and architecture for assessing distributed and load centric control objectives, e.g. power and energy management strategies.
Reliance on CPS in critical infrastructure has led to research at CAPS in the area of CPS security. Although progress has been made with respect to advanced power electronics and controls, greatly increasing capabilities, critical gaps remain with respect to CPS security. Identification, reasoning, and response to cyberattacks are completely different than traditional, physical system faults. With multi-domain simulation capabilities CAPS is uniquely positioned to probe, design, and test systems for CPS security-related challenges.
View the Integrated Distributed Controls and Cyber-Physical Hardware-in-the-Loop Test Bed setup
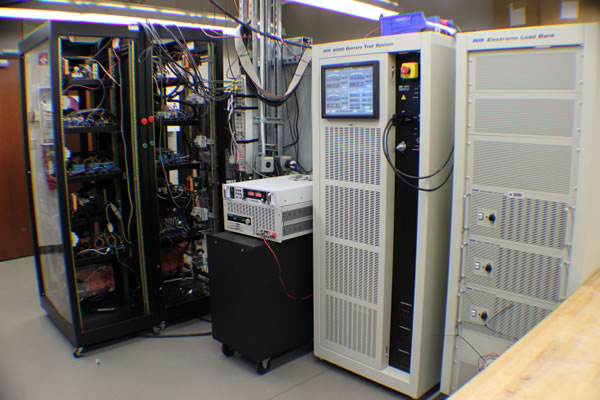
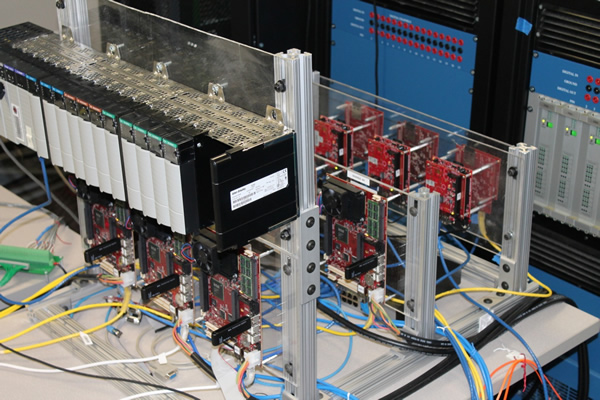
High Electric Field Lab (HEFL)
Electrified transportation, aerospace, renewable generation, industrial plants and even T&D are under impetuous renovation changes as regards electrical and electronics components. Unprecedent stressing conditions, aiming at improving specific power, efficiency, effectiveness, reliability, in extreme environments as regards power quality, electrical and mechanical stress, temperature, voltage levels and waveforms, put in danger reliability, availability, safety and long-term performance of a fundamental part of an electrical and electronic component, i.e. electrical insulation. Breakdown of electrical insulation, indeed, is one of the major causes of electrical asset failure and system outage.
The High-Electric Field Lab focuses on the development of innovative technologies to devise new materials, design techniques, diagnostics, specification, condition monitoring of electrical insulation systems for any type of electrical and electronics component and any voltage waveforms. Voltage levels available in te lab are up to 100 kV, with AC sinusoidal, AC modulated, DC and multi-function generators, temperatures up to 400 °C, low and high-pressure chambers (from 20 mbar to 10 bar), environmental factors of influence (as humidity). Tools for material characterization and high-field conduction current and space charge, supported by microscopy, as well as the most advanced worldwide software and hardware for partial discharge measurements and monitoring are available at HEFL.
The approach to R&D projects at HEFL takes into account material and phenomena physics investigation and modelling to on-field application. Scalability, broad applications, first reaction to new materials, processes, designs and operation issues are addressed with unique lab capabilities and approaches.